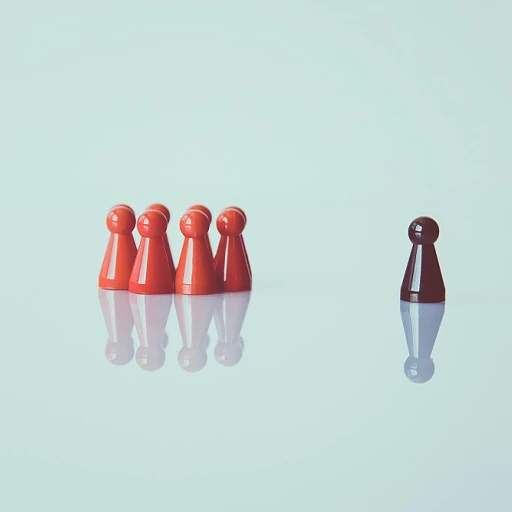
The Impact of Automation and AI on Workforce Demand
Automation and AI: Shaping the Demand for Workforce
The manufacturing industry is witnessing a seismic shift in the demand for workforce due to the rapid integration of automation and artificial intelligence (AI). These technological advancements have reshaped traditional roles and created new opportunities, yet they have also introduced unique challenges in staffing and talent acquisition.
Automation has become indispensable for companies looking to optimize their operations and enhance efficiency. Smart factories and AI-driven processes are revolutionizing how goods are produced, leading manufacturers to rethink their staffing strategies. While certain manual tasks are being automated, the demand for a modern workforce equipped with technical and digital skills is on the rise. This shift necessitates a reevaluation of the skill sets required in modern manufacturing environments.
As future work partners play a crucial role in shaping the new industrial workforce landscape, manufacturers must explore diverse strategies to attract and retain talent. In doing so, they address workforce changes and ensure the constant availability of skilled labor.
Deloitte's insights into manufacturing indicate that industries must adapt to labor market trends and anticipate skills gaps that will affect future staffing needs. This means investing in continuous learning and development opportunities for employees, as well as adopting flexible work arrangements to stay competitive. The manufacturing institute and staffing agencies are vital in bridging these skills gaps by offering targeted training and upskilling programs.
The focus on automation and AI not only impacts the immediate staffing needs within the manufacturing sector but also sets the stage for long-term adjustments in workforce planning. Companies and local businesses must establish partnerships with industrial staffing solutions to ensure they meet the evolving demands of the industrial workforce.
Emerging Skill Sets for the Modern Manufacturing Workforce
The Skill Revolution in Manufacturing
In the rapidly evolving landscape of the manufacturing industry, the demand for a new set of skills is more critical than ever. As automation and AI reshape the traditional roles of manufacturing workers, there's a growing emphasis on acquiring new technical and digital competencies to remain competitive and relevant.
As companies in the sector integrate more technology into their operations, the skills gap widens. The Manufacturing Institute highlights the importance of bridging this gap by upgrading workforce competencies to handle sophisticated technology and data analytics. This shift calls for a more tech-savvy workforce, and as a result, manufacturing staffing needs are being redefined.
Manufacturers, now more than ever, require employees who are not just skilled in traditional roles but are also fluent in new-age skills like programming, data analysis, and machine learning principles. This creates a vibrant opportunity for job seekers looking to transition or advance in the manufacturing sector as the demand for hybrid skills continues to rise.
The industry is responding to these needs by collaborating with educational institutions and staffing agencies to design specialized training programs. Staffing solutions offered by agencies and local business initiatives focus on developing a workforce equipped to handle the challenges posed by modern manufacturing, thus ensuring significant staffing resilience.
Moreover, deloitte's research into the future of industrial staffing indicates that mastering these emerging skills will be pivotal in overcoming labor shortages that the United States manufacturing sector might face in the coming years. Manufacturers and agencies are urged to invest in their current employees’ skill development while seeking fresh talent adept in these critical areas.
As we navigate through these changes, it's essential to view industrial staffing as an evolving landscape, where both current and incoming workforce members should be equipped with a dynamic skill set to meet the demands of a tech-driven business environment.
Adapting to Demographic Shifts in the Workforce
Adjusting to Workforce Demographics
The labor market within the manufacturing sector in the United States is experiencing significant demographic changes. Many organizations are finding that adjusting to these shifts is crucial to address current and future staffing challenges effectively. As manufacturers strive to maintain a skilled workforce amidst aging employees and a limited supply of young talent, they need to develop proactive strategies. For businesses, adapting to demographic shifts involves several key considerations:- Diverse Employee Groups: Manufacturers must cultivate an inclusive environment that attracts a wide range of talent. By targeting diverse demographics and collaborating with staffing agencies, companies can tap into a broader talent pool and address labor shortages effectively.
- Knowledge Transfer: The aging workforce implies that a substantial amount of industry expertise may retire with senior employees. To mitigate this, businesses should implement robust mentorship programs to facilitate the transfer of knowledge, ensuring continuity in operations and maintaining institutional excellence.
- Regional Initiatives: As labor shortages vary across different locales, companies should tailor their recruitment and workforce development strategies to local demographics. Understanding regional labor markets and emerging local trends can guide manufacturers in designing effective staffing solutions that align with community-specific needs.
- Generational Shifts: Addressing generational differences involves recognizing the motivations and work preferences of younger employees. Offering roles that provide career growth, integrating technology, and accommodating flexible work arrangements are some ways manufacturers can appeal to Millennials and Gen Z workers.
Flexible Work Arrangements and Their Role in Manufacturing
Embracing Flexible Work Models in Manufacturing: A New Workforce Paradigm
The traditional 9-to-5 work structure has been a cornerstone in many industries for decades, but now, manufacturers are increasingly recognizing the value of flexibility as a strategic advantage. As the other sections have discussed, the landscape of manufacturing is shifting, driven by automation, emerging skill sets, and demographic changes. This context sets the stage for flexible work arrangements to play a pivotal role in addressing labor shortages and attracting talent. Manufacturers are beginning to explore different staffing models to remain competitive in a tight labor market. Implementing part-time roles, job sharing, and remote work for certain positions can provide both employees and the industry alike with the adaptability needed to thrive in the modern era. The adoption of these flexible work arrangements can also help bridge the skills gap by attracting individuals who might otherwise be excluded from the traditional workforce. For example:- Part-time work opportunities: This allows those who may need to balance other commitments, like family or continued education, to enter the workforce on terms that suit their needs.
- Job sharing: This concept permits two employees to share responsibilities of a single full-time position, bringing together a pair of skills that may be hard to find in one individual.
- Flexible hours and shifts: Offering varied schedules can appeal to a more diverse workforce, including parents, students, and those seeking a better work-life balance.
The Importance of Continuous Learning and Development
Fostering a Culture of Lifelong Learning
In the rapidly evolving manufacturing industry, continuous learning and development are not just buzzwords; they are essential strategies for maintaining a competitive edge. As automation and AI reshape the landscape, manufacturers must prioritize upskilling their workforce to bridge the skills gap and meet new staffing demands. This approach not only addresses labor shortages but also enhances the overall capabilities of manufacturing workers.
Manufacturers are increasingly recognizing the need for robust training programs that align with the latest technological advancements. By investing in employee development, companies can cultivate a workforce adept at handling sophisticated industrial products and processes. This is particularly crucial as the industry navigates demographic shifts and the influx of younger employees who value growth opportunities.
Leveraging Technology for Skill Enhancement
Technology plays a pivotal role in facilitating continuous learning. Online platforms and virtual training modules offer flexible solutions for employees to acquire new skills at their own pace. This flexibility is vital in a sector where traditional work arrangements are giving way to more adaptable models. Moreover, partnerships with educational institutions and staffing agencies can provide tailored training programs, ensuring that the workforce remains aligned with industry needs.
Companies like Deloitte Manufacturing have highlighted the importance of integrating digital tools into training initiatives. These tools not only enhance learning experiences but also help track progress and identify areas for improvement. By fostering a culture of lifelong learning, manufacturers can ensure their employees remain engaged and motivated, ultimately leading to higher retention rates.
Creating Pathways for Career Advancement
Continuous learning should also be linked to clear career progression paths. Employees are more likely to stay with a company if they see opportunities for advancement. Manufacturers can benefit from developing structured career pathways that reward skill acquisition and performance. This approach not only helps retain talent but also attracts job seekers looking for long-term growth in the manufacturing industry.
In conclusion, the future of work in manufacturing hinges on the ability of companies to adapt to changing demands through continuous learning and development. By prioritizing skill enhancement and creating clear career pathways, manufacturers can build a resilient workforce ready to tackle the challenges of tomorrow.
Strategies for Attracting and Retaining Talent in Manufacturing
Enhancing Talent Attraction and Retention
To sustain progress in the manufacturing sector, companies are focusing on effective staffing strategies that aim not only to attract but also retain skilled workers. One of the main tools in achieving this is by bridging the skills gap. This helps businesses address labor shortages in a competitive job market. With the rapid evolution of the industrial landscape, manufacturers can take several steps to enhance their appeal to job seekers:- Leverage Local Partnerships: Building relationships with local educational institutions and training centers can create a pipeline for emerging talent. This collaboration allows businesses to influence curriculum and ensure that industry-relevant skills are being taught.
- Utilize Staffing Agencies: When it comes to staffing solutions, partnering with staffing agencies is crucial. These agencies offer expertise in connecting businesses with the right talent, especially for companies navigating labor shortages in the United States.
- Offer Competitive Packages: To stand out in the industrial staffing market, manufacturing firms need to offer competitive salary packages and benefits. This not only attracts top talent but also improves employee satisfaction and loyalty.
- Invest in Employee Development: Encouraging continuous learning and development shows that a company values employee growth. This can include skill enhancement programs, workshops, or support for further education.
- Create a Positive Work Environment: A supportive workplace culture can improve employee retention. Employees who feel valued and engaged are less likely to seek opportunities elsewhere.